FUME TREATMENT PLANT
Fume treatment plants are types of equipment that are manufactured to solve the problem of controlling environmental pollution in any type of industry. The range of products are as follows:
- High Temperature Ceramic Filters
- Wet Scrubbers
- Bag Filters
- Selective Catalytic Reduction (SCR)
- Selective Non-Catalytic Reduction (SNCR)
- Volatile Organic Compounds (VOC) Removal
- De-sulfurization plants
- Vacuum Cleaning Systems
- Dry and Semi-dry Gas Absorption
- Regenerative Thermal Oxidation (RTO)
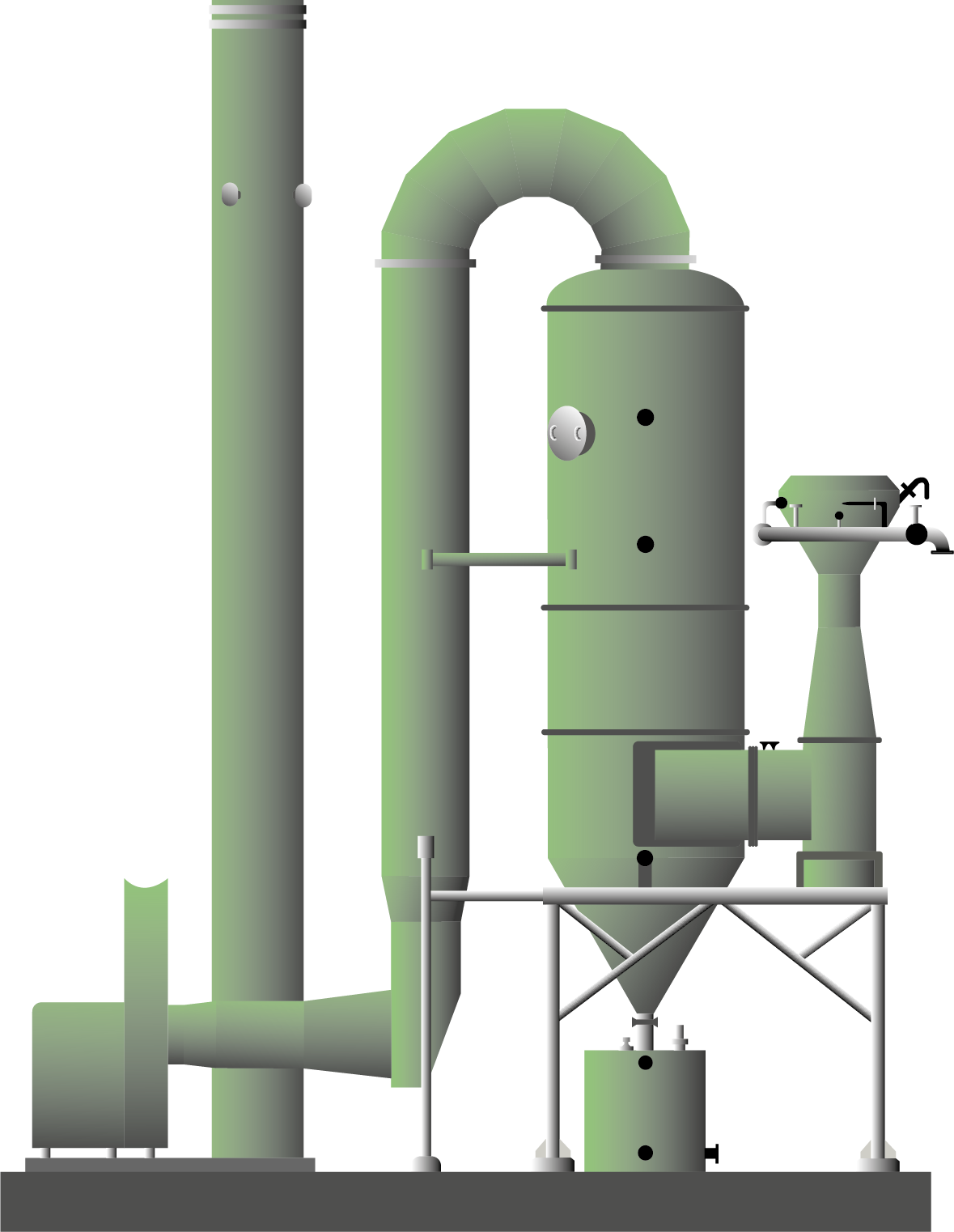
AIR POLLUTION CONTROL SYSTEMS
BAG FILTERS
Part of the dust which arrives with the gas is separated in the entrance of the filter. The rest of the dust is taken on the surface of the bag, where an indispensable dust precoating is created to obtain high standards of separation. The filter bags are cleaned by periodic pulses of compressed air, which goes to the jet pipes through the opening of the membrane valves. Each row of bags is blown creating a strong pressure increase in the interior of the bags. As a result, the dust settled on the outside of the bags falls. The membrane valves are electronically controlled allowing the adjustment of pulse time and cycle to the conditions of the desired operations. The electronic controller can be operated manually or automatically commanded by the pressure loss. The automatic controller maintains constant the pressure loss of the filter. The FIVEPULSE filters can be made of vertical bags or horizontal bags. These last ones are used when there is height limitation for the extraction of bags. In the vertical filters, the gas entrance can take place by the hopper or by a side of the filter casing. In the horizontal filters however, it takes place by the top part. There are four series of FIVEPULSE filters- SQUARE SERIES
- RECTANGULAR SERIES
- DOUBLE SERIES
- INDEPENDENT CHAMBERS SERIES
COMPACT FILTER
The compact filters designed by FIVEMASA are cleaned by periodic pulses of compressed air and they are designed to work continuously and minimize residual emissions. Because compact filter provides maximum filter area in a minimum space, the volume of the filter housing can be reduced considerably and so the occupied area. The air charged with dust enters to the filter top or laterally, the filters allow to pass the clean air to the front side of the filter. The dust falls down into the hopper after the cleaning through periodic pulses of compressed air and discharge via a rotary valve or screw conveyor plus rotary valve. The air with dust enters to the head of the filter housing and clean air goes out through the frontal side of the filter, soothe down flow facilities the dust to fall down into the hopper.ELECTROSTATIC PRECIPITATORS
As contaminated air enters the electrostatic precipitators it must pass by speak electrodes. The AC voltage creates a high intensity field wherein the particulate matter in the air becomes electrically charged. The charged particles then pass into a collector plate section which attract and collect. Liquid contaminants coalesce into droplets and run-off the collector plates in a self-cleaning action.SCR (SELECTIVE CATALYTIC REDUCTION)
The primary difference between SNCR and SCR is that SCR employs a metal-based catalyst with activated sites to increase the rate of the reduction reaction. A nitrogen based reducing agent (reagent), such as ammonia or urea, is injected into the filter system or downstream the filter system. The reagent reacts selectively with the flue gas NOx within a specific temperature range and in the presence of the catalyst and oxygen. For the majority of commercial catalysts (metal oxides), the optimum temperatures for the SCR process range from 250 °C to 427 °C.SNCR (SELECTIVE NONCATALYTIC REDUCTION)
SNCR is based on the chemical reduction of the NOx molecule into molecular nitrogen (N2) and water vapor (H2O). A nitrogen based reducing agent (reagent), such as ammonia or urea, is injected into the post combustion flue gas. The SNCR process occurs within the combustion unit which acts as the reaction chamber. Reagent is injected into the flue gas through nozzles mounted on the Wall of the combustion unit. The injection nozzles are generally located in the post-combustion area, the upper area of the furnace and convective passes. The injection causes mixing of the reagent and the flue gas. The heat of the boiler provides. Wet ProcessSCRUBBERS TYPE VENTURI
The venturi filters are designed with wet entrances for high temperature gases, or dry for saturated or cold gases. They can have a fixed section for a constant air flow and adjustable for a variable air flow. They can be built in reinforced polyester with fiber glass, stainless, normal, covered by rubber in the inside. They are used to capture very small particles and its filtration efficiency is comparable to those of electro statistic precipitators and filter bags. However, the installation cost is lower.MEDIUM ENERGY SCRUBBER FIVESPRAY AND DYNAMIC
The filtration efficiency of this two equipment is similar, but lower than the venturi filters. The pressure loss is between 125 and 200 mm.w.g. FIVESPRAY can be built with and extracting drag incorporated, meanwhile the second one can't. Its utilization depends on the application and the requirements of the clients.DROPLET SEPARATORS
By means of bended profiles, we get the elimination of droplets on vanes by inertial forces. The eliminated liquid film is drain aged to the lower part of the unit, getting out from the assembly device. Depending on the nature of the gas we can supply single stage or multi-stage droplet separators with or without flushing systems.AIR POLLUTION CONTROL SYSTEMS
Design and manufacture of below projects, in any type of industry.- Industrial cleaning plants
- Centrifugal and axial fan silencers
- Anti-noise cabins
- Micronizing and drying plant
- Climatization and ventilation
- Milling and classifying
TIPYCAL APLICATIONS:
- Behind gas scrubbers
- Spray towers
- Air conditioning
- Air and gas cooler